[Case study] Wrap case packing of Doypack bags
Context
Our client prepares and sells ready meals based on fried and whole vegetables. These products are packaged in Doypack bags. During the packaging process and after pasteurization, the Doypack vegetable bags are packaged in cardboard boxes. The client now wants to automate this packaging process, which has been done manually until now, using an automatic wrap case packer.
Technical characteristics of the products:
- Vertical Doypack bags
- Product rate: 320 bags/min
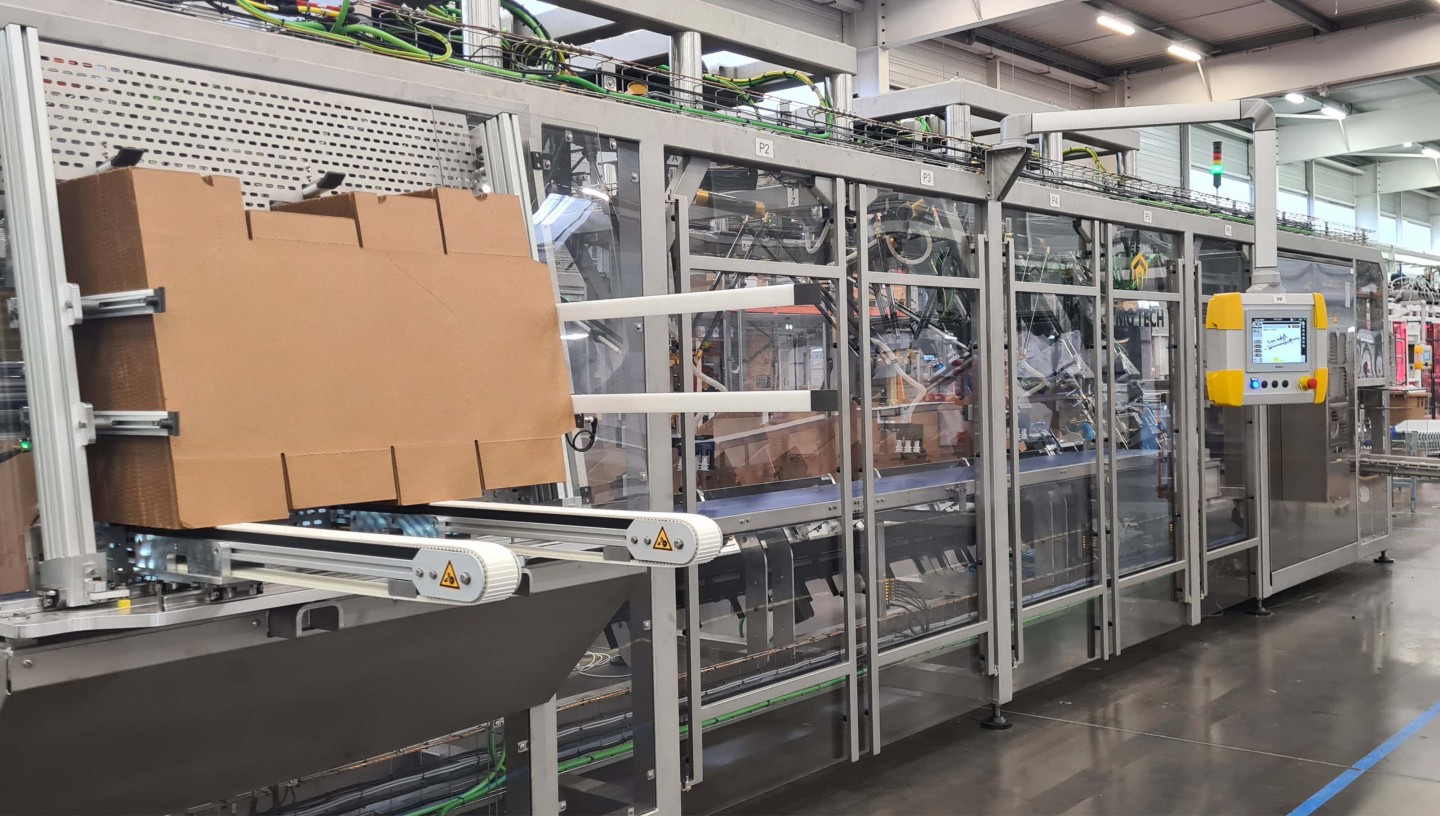
Solution proposed and provided by MG Tech
As requested by the client, MG Tech proposed and designed a wrap case packer solution. To meet the product rate of 320 bags/min at the production outlet, MG Tech provided two wrap case packers, each receiving 160 doypacks/min with the bags arriving in 2 lines on each machine. The products are picked up by Delta robots and in pairs, allowing 24 bags to be packaged per box.
The main functions of the wrap case packers are:
- Receiving and checking Doypack vegetable bags using a vision system, allowing the positioning and height of the bag to be checked
- Forming the cardboard case as the products are boxed
- Closing the case with a lid
- Checking the conformity and gluing of the case as well as the weight of the case and the number of bags inside
Technical characteristics of the case packers:
- Speed of each machine: 160 bags/min
- Product arrival on two conveyor lines
- Packaging of 24 bags per case
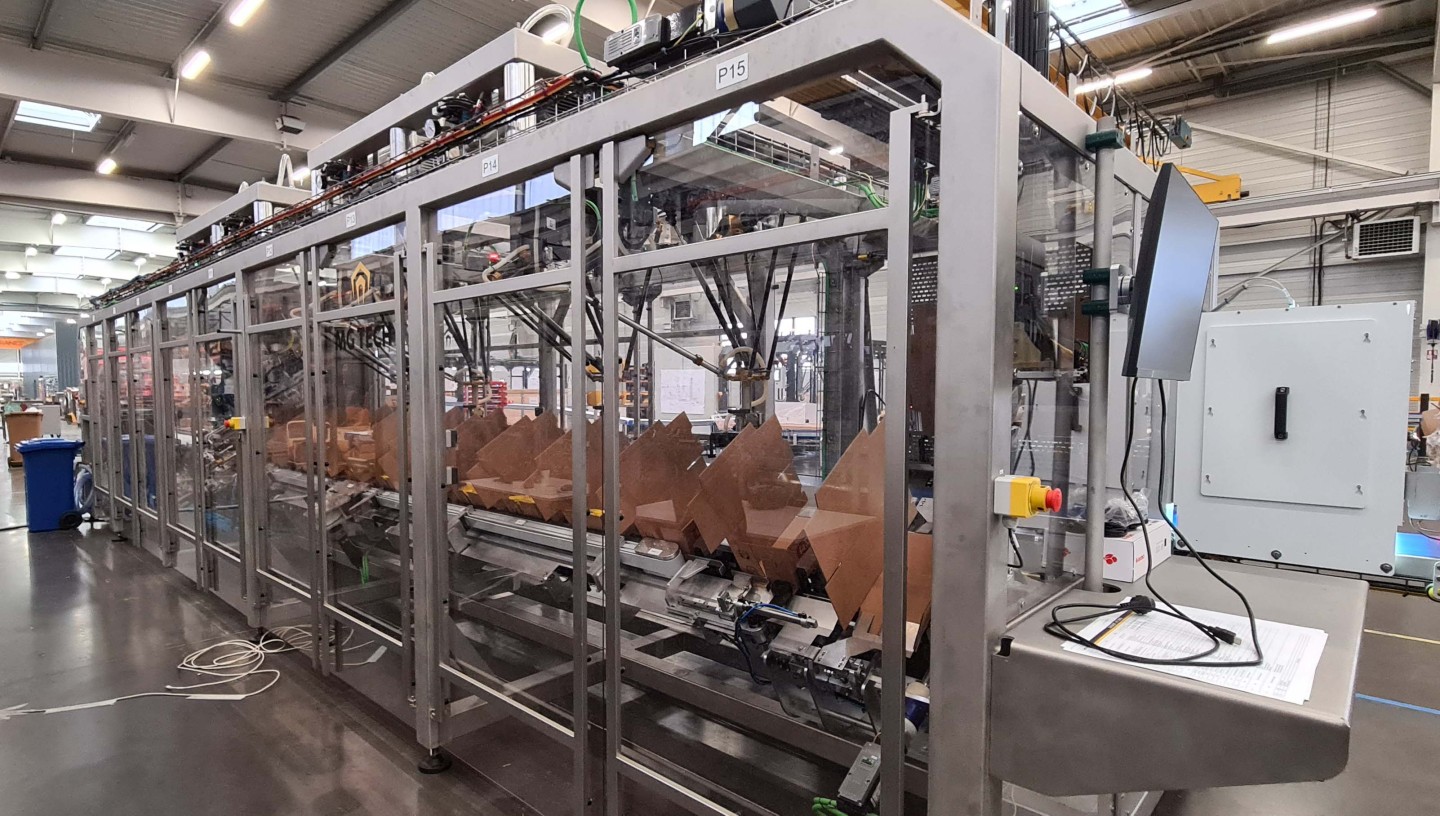
The advantages of the MG Tech solution
Collaborative project management
MG Tech supported the client during the transformation of its packaging from a RSC case to a Wrap-around case. The main discussions focused on the VRC (Vertical Resistance of the case), its mechanical assembly and the predisposition to a pre-cut for ready-to-sell.
Respect for the integrity of the products handled
The Delta Pick & Place robot technology offered by MG Tech allows for a minimum of contact with the products and handling. The products are conveyed on the conveyor belts and are directly placed upright in the cardboard cases using Delta robots equipped with suction cups. No grouping of products is necessary upstream, which avoids additional handling of the bags. This advantage was decisive for the customer in its choice of technology because it had already previously faced mechanical systems that greatly damaged the products when they were packed in the case.
A case transfer adapted to the product
Since the customer's product can vary and has a fairly liquid structure, its behavior once upright is incompatible with a standard case transfer. To overcome this phenomenon, we recreated the packing conditions used to date by our customer's operators. A case tilting system has been integrated into the case packer to facilitate the storage of products inside the case and to hold them securely when folding and gluing the flaps, while taking care of the bags.