[Case study] Automation project for a complete pasta packaging line
Context
Our customer, already equipped with several MG Tech machines for packaging pasta bags, called again on our teams to design and supply new machines to increase the production capacity of its production unit. The goal was to integrate a fourth packaging line, but with high-speed case packing and palletizing equipment.
At the same time, the client wanted to review the management of its pallet packaging circuit.
Product technical features:
- Flat-bottom bags of various weights (300g to 1kg)
- Bags arrive on two flat lines
- Two types of cases: dihedral and shelf-ready cases
- Packaging in 4 or 9 bags, upright in the cases
Equipment technical features:
- Product rate: 188 bags/min
- Case rate: 22 cases/min
- 16 product formats, 3 case formats and 30 packaging format
- 60 pallets/hour
EQUIPEMENT TECHNICAL FEATURES:
To meet the customer's needs, we provided a complete solution from product delivery to finished pallet removal.
Wrap case packing:
To optimize this packaging line, our teams designed and manufactured a wrap case packer that accommodates different case types and formats: dihedral cases and shelf-ready cases with 4 corners glued. The unique feature of this wrap case packer is the addition of an automatic supply of cardboard blanks via a depalletizer.
The pallet of cardboard blanks is integrated directly into the case packer, and a robot unstackers batches of cardboard blanks, placing them at the beginning of the wrap case packer. This significantly reduces handling for the operator. The wrap case packer performs upright case packing of pasta bags using 5 delta robots that load the products into the cases. In addition, a vision system controls the weight of the cases to remove them that are too heavy or too light.
Robotic palletizing:
The objective of the new palletizer is to improve production rates, ensure stable palletizing, and facilitate format changeovers for different products.
We have integrated a high-performance palletizing system based on a 4-axis polyarticulated robot. This allows for layered palletizing, ensuring optimal placement of full cases on the pallets. This palletizing system integrates interlayer placement to ensure pallet stability and the management of around ten palletizing recipes to manage different formats. This complete automation reduces operator intervention and increases productivity.
Intelligent pallet handling using mobile robots
The packaging line also features Evobot mobile robots, designed and manufactured by MG Tech.
The three turtle AGVs are equipped with conveyors and lifters, allowing the AGV's height to be adjusted to match our client's conveyors for efficient pallet evacuation.
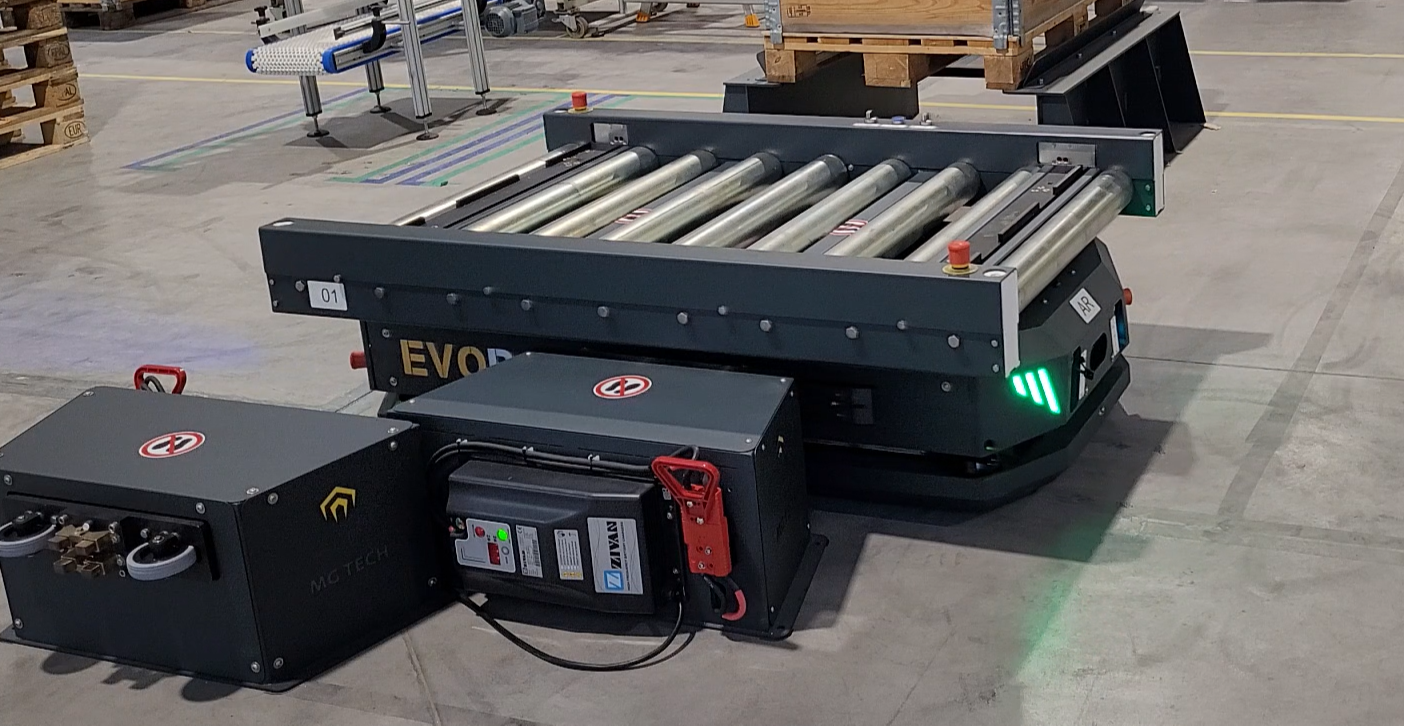
These mobile robots recharge themselves whenever they're not in use, thanks to charging stations, to optimize their charge.
This new equipment manages the flow of the four production lines, with a production of 50 to 60 finished pallets per hour. The finished pallets are collected by the turtle AGVs and taken to the entrance of the wrapping line. Once wrapped and labeled, the pallets are removed to the logistics area and then loaded onto trucks for secure transport.
At the same time, the turtle AGVs supply the palletizers by retrieving stacks of pallets from the workshop's inventory. This allows us to optimally utilize the capacity of these mobile robots within the production floor.
Integration of additional equipment
The end of the line incorporates a turntable stretch wrapper capable of filming up to 60 pallets per hour and a labeler (supplied by the customer) positioned on a turntable to label multiple sides of each pallet.
THE ADVANTAGES OF THE MG TECH SOLUTION
Productivity gains
Thanks to this solution, the client improved the efficiency of its packaging process with a case packer adapted to high-speed case packing of bags. This allows the client to package these products in various formats without requiring operator intervention.
Furthermore, thanks to the integration of a cardboard blank depalletizer, the operator no longer needs to load the cardboard blanks into the case packer magazine; they simply place a full pallet upstream of the machine. This reduces the risk of musculoskeletal disorders, allowing the operator to focus on other tasks.
Connected Machines
All the machines included in this end-of-line packaging system communicate with the client's ERP system. This allows for better production monitoring, greater responsiveness, and product traceability throughout the chain.
New pallet flow management
The addition of a new production line at our client's facility brought a new approach to organizing the flow of pallets exiting the palletizers on its four production lines, which had previously been managed manually by operators.
Our team therefore proposed automating the flow of finished pallets to transport them to the wrapping and labeling line using a mobile robotics solution.
Handling by AGV mobile robots allows full pallets to be transported from the palletizer exit to the wrapping line.
This shift from manual pallet flow management to full automation offers a real advantage within this production unit, allowing it to handle larger volumes and significantly increase productivity.
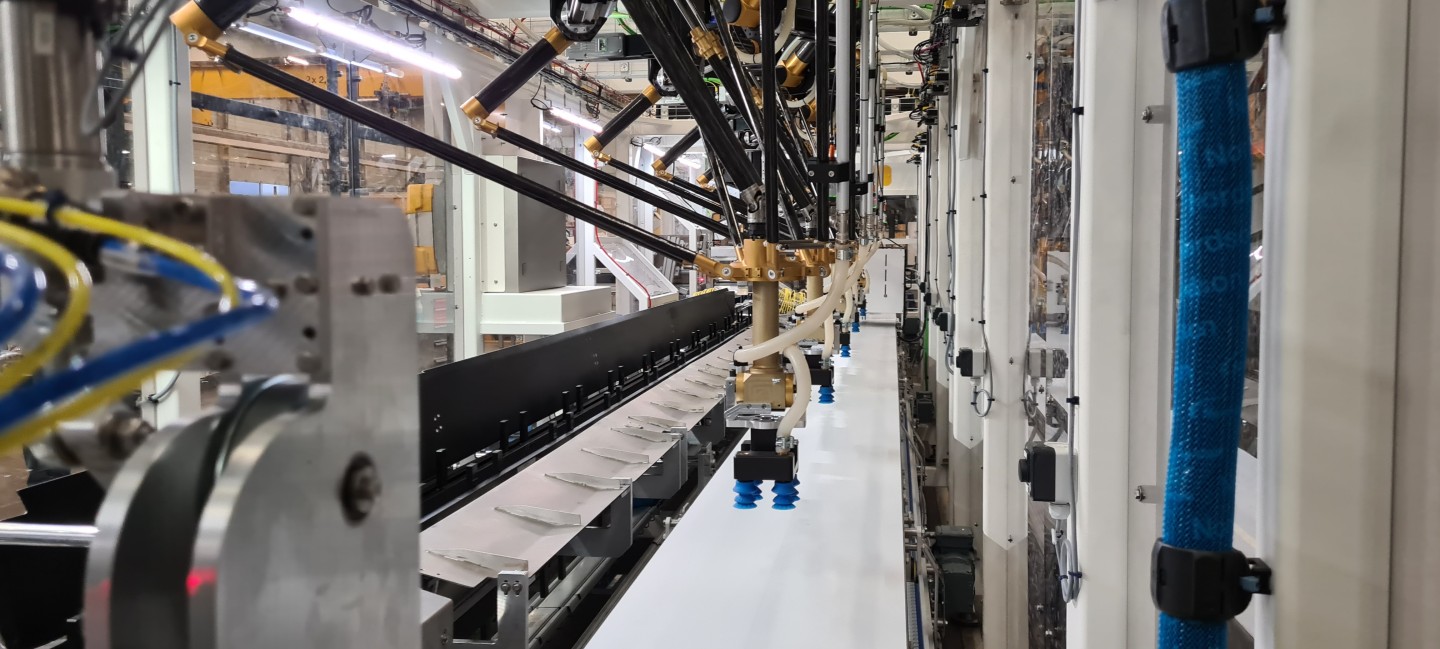